We are passionate about providing the world with sustainable low-carbon solutions for a greener, stronger and smarter future. From electrical wiring in homes and offices to building electrical vehicles, our aluminium and copper are extensively used across industries in making products that improve lives.
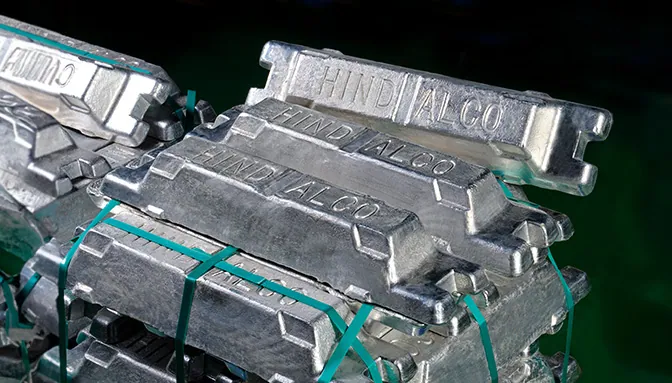
Aluminium
We cater to a variety of market segments by offering customised value-added aluminium-based solutions. From supplying aluminium to railway coaches and automobiles used by millions of people every day, to the kitchen foil that keeps your food warm, our products are present in every aspect of people’s lives.
Read more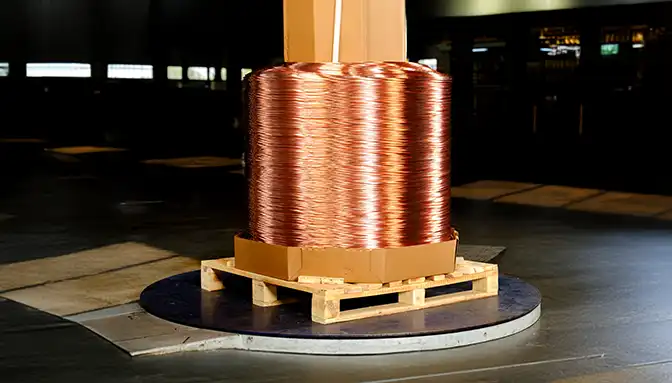
Copper
Our copper division, Birla Copper, ranks among the world’s top three copper rod players. We produce LME-grade copper cathodes, continuous cast copper rods and precious metals like gold and silver. Our copper is used in the manufacture of consumer durables, automobiles and electrical vehicles, as well as in wiring and electrification.
Read more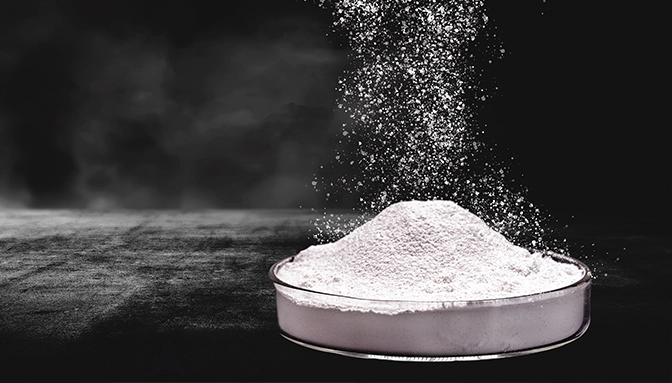
Specialty alumina
Hindalco’s specialty alumina business focuses on special alumina and alumina hydrates which are manufactured in-house. Our specialty alumina business serves customers across 32 countries and has multiple industrial applications in advanced ceramics, polishing, refractories, water treatment and as fire-retardant fillers.
Read more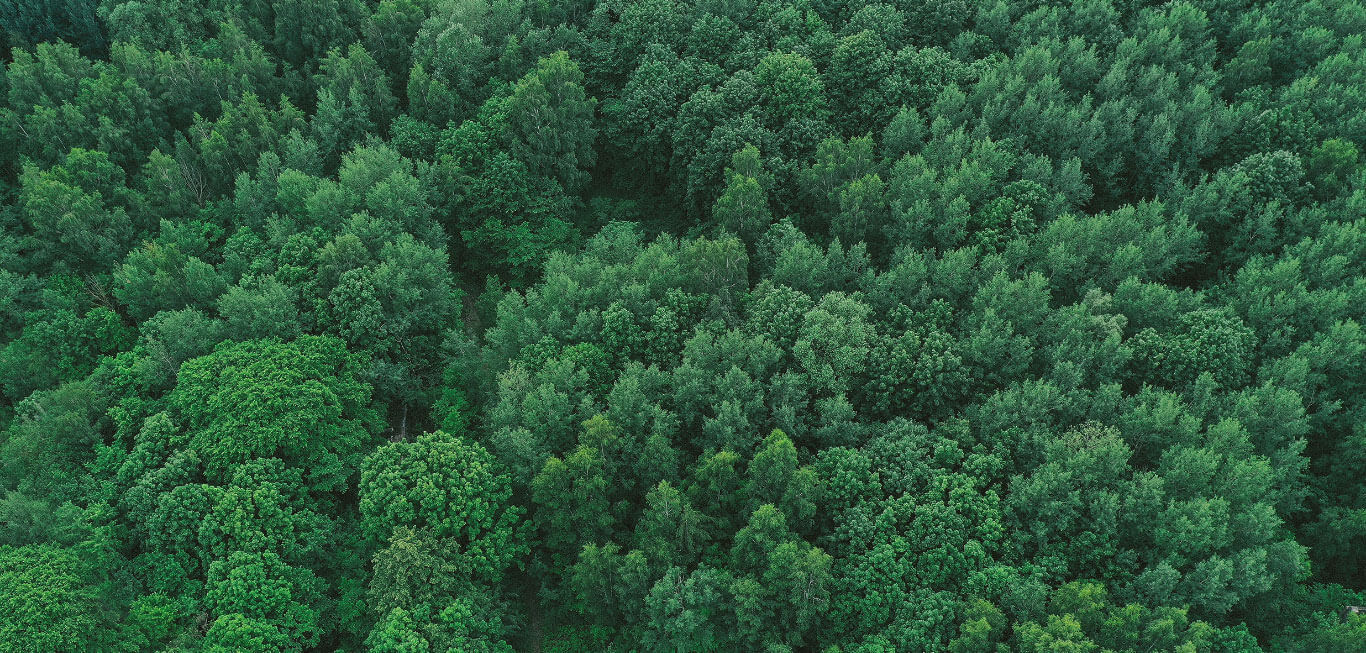
Our commitment to sustainability
Sustainability is at the heart of everything we do. We have set holistic targets across four sustainability axes of emissions, water, waste and biodiversity, and we plan to achieve these targets by adopting green-tech, circular innovations.
Since 2020, we have been continually ranked at the top of the aluminium sector for our sustainability-led performance. We have been recognised for three consecutive years as the World’s Most Sustainable Aluminium Company by the S&P Dow Jones Sustainability Indices Corporate Sustainability Assessment rankings. We have partnered with IUCN to implement biodiversity management initiatives at several of our sites which has resulted in growing the cumulative green belt by 10%. As an organisation, we strive to adopt greener, stronger and smarter processes every step of the way, and we are proud of what we have accomplished so far.
Read moremw
of renewable energy capacity has reduced emissions and dependence on fossil fuels
million
GJ energy savings
%
waste utilisation
%
reduction in specific GHG emissions from FY 2011-12*
M3 water storage capacity created in water stress areas*
trees planted*
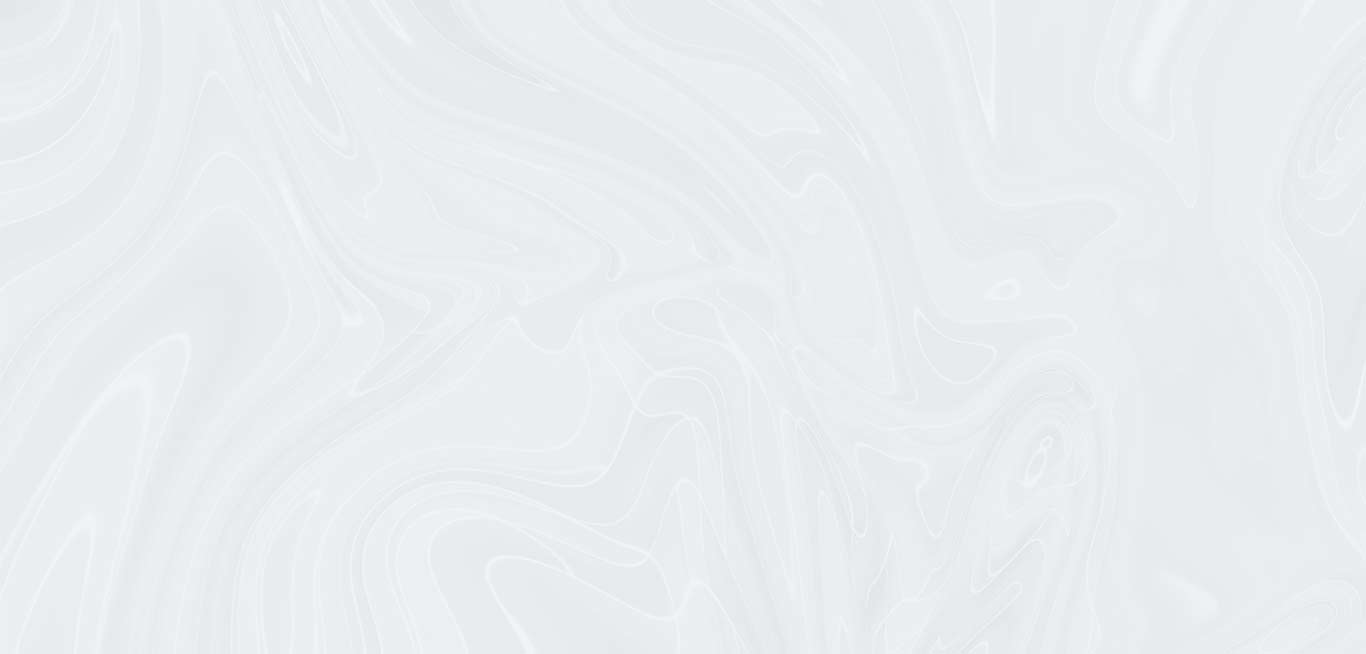
Moving towards Industry 4.0
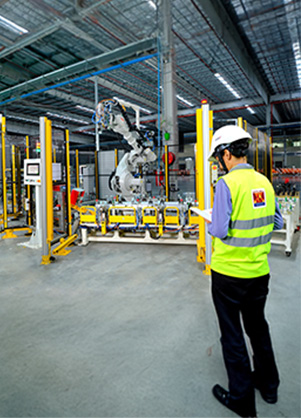
Robotics
We are leveraging new technologies to improve our process efficiency and optimise resource consumption. As we progress towards the digital era of Industry 4.0, we have adopted several mechanical and robotic automations to improve our productivity. Our team is continuously working with leading robotic solution providers in the industry to automate more processes.
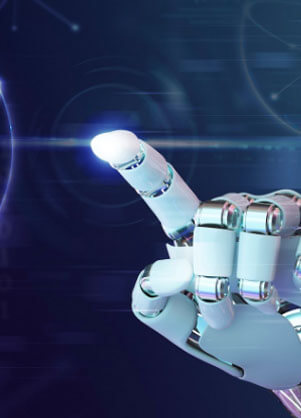
Artificial intelligence
Hindalco also makes use of artificial intelligence in maintaining its manufacturing equipment. We attach digital sensors to our equipment that collect data, analyse data and predict failure. A machine learning algorithm understands how the equipment responds to variation in processes, and triggers an alert whenever it predicts a failure.
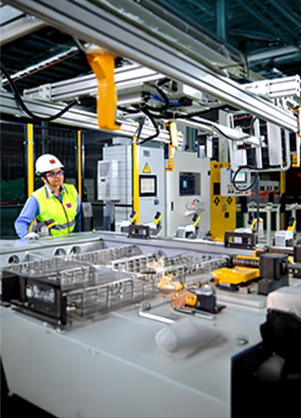
Digitisation
Birla Copper has implemented the acoustic steam leak detection system. It detects sound waves from a steam leak and transforms them into an electronic voltage signal, which is then amplified, filtered and processed. ASLD helps the team understand the severity of the leak as well as the location so that damages can be minimised.
For suppliers and vendors
For queries
Existing suppliers/vendors
Useful documents
Hindalco supplier code of conduct